Breaking New Ground
- Kimi BrownKawa
- Jul 16, 2020
- 6 min read
Updated: Nov 26, 2022
Chip and I are excited to report that we have broken ground on the first ever fully permitted tire bale home in New Mexico!
What does that mean? It means that we will be repurposing about 9000 tires from a landfill to build the 5-foot-thick exterior walls of a little passive solar off-grid home.

To manage hundreds of thousands of tires and decrease the perennial dangers of mosquito breeding and fire hazard inherent with tire storage, landfills compress about 100 tires into a large bale bound with strong wire. Each bale at our local Red Rock Landfill, is about 4’ x 5’ x 2.5’ and weighs on the order of 2000 pounds. Compressed in this way, the bales can be stacked neatly, pyramid style. Tire bales have been used in some civil engineering projects, such as erosion control. Still, the rows upon rows of compacted bales stacked three high take up a huge amount of space, and spent tires continue to flow into landfills at an unmanageable rate. Wouldn't it be great if those tires could turn into houses? One of the long sections in the photo above could make five houses the size of ours.
Almost a year ago now, I wrote the blog post Future Digs? which detailed how we came to the decision to build a tire bale home in the first place. Last August we got the engineering plans from Precision Structural Engineering, and thought we might be on our way! (PSE now has added a page devoted to tire bale building, by the way, featuring a future home we all know and love!)
...but as you may know if you’ve been reading our blog, we did end up living in our popup camper throughout last winter, and that’s where I still sit as I write this (while Chip makes dinner outside on our propane stove). Here are our house-building milestones since that August Future Digs? post.
July, 2019 -- We got an estimate for a general contractor to take on the entire build, since winter was coming so soon. The estimate was well beyond our budget, but that doesn’t mean it was unreasonable -- the project has so many unknowns; any contractor would have to play it safe estimating such a job.
August -- We decided we needed to wait until after winter to tackle the house. That gave us time to settle into the community, get to know folks, and just catch our breath from the move and life change. We figured that starting in the spring would give us time to take on more of the work ourselves.
September -- We decided to build a greenhouse -- Our theory was that this "quick and easy" first step would at least give us a warm place to hang out on those cold winter days… but by the time we got it closed up, the weather was already starting to warm! Everything takes longer than you think…
November -- We held off on getting our building permit until we saw how things went with the greenhouse.
March -- We applied for our house permit when the greenhouse was well underway and going smoothly -- but it was at the outset of a pandemic!
May -- Although it took almost two months rather than the normal 7-10 business days, the building permit did finally come through.
Permit in hand, we contacted our friend Bill, who had helped us with the greenhouse earthmoving work. He and his crew have been helping us prepare the site and foundation to meet the engineering specs. Here's what we've done so far...
Leveling the site, Randy hit big rocks early on, challenging the Bobcat. We decided to go with a bigger machine, and he was back on it a couple days later with a big excavator. They cut the site into the hill to the north, so that we’d have a natural berm at the back, and so that the tire bales would have a solid foundation to rest on (rather than the sandy top layer or fill). Buddy and Orie spotted Randy’s work, removed the dirt piles using the Bobcat, and checked for level throughout. Randy used much of the removed dirt to fill in the “front yard” and greenhouse area level with the house floor, and stockpiled the rest for our future work making earthen plaster and floors.
Chip and I visited the landfill twice to measure the bales and determine the variability from bale to bale. Since the bales are not exactly uniform, we had to make plans taking into account the minimum and maximum possible sizes. We'll have wider concrete channels than necessary, especially for the eastern side wall, since the wall may be more to the west (if we average small bales) or more to the east (if we average large bales), so we have to be ready for either placement. As our own general contractors on the job, we had to calculate materials needs(bales, concrete, gravel, and rebar) and plan layouts. We measured and marked off the house footprint at the start of the project, and again after the whole site had been leveled.
Then Randy dug the trenches. We had requested that the engineers (Precision Structural Engineering) use the minimum concrete possible, so rather than a slab, we’ll have concrete only under the bales and at each support post. The engineering plans call for 1’9” of compacted rock as a base for 12” of concrete, so the trenches in this rocky soil were dug 2’9” deep below the cutaway site level! Luckily we did not hit bedrock… They did bring up a nice log of petrified wood, which will one day be a a little side table in our yard -- or on the west patio, which is pretty much where this tree grew a couple hundred million years ago!
Next we brought in crushed rock from a neighbor's gravel quarry (Chip and I waited at each end to open the gates so Randy could make the gravel runs more efficiently), and the guys spent a couple of days filling the trenches back in and compressing the rock with a compactor. They built forms and laid out the reinforcing rebar, and then we had a week’s stoppage waiting for wire mesh to be delivered. The wire mesh will be embedded in the concrete, and will emerge to wrap around the tire bales as a stucco base (again, per engineering plans). Wednesday we (Buddy, Orie, Chip, and I) started in again and put the wire mesh in place, leaving just a couple of hours of work for the guys to finish up this morning.
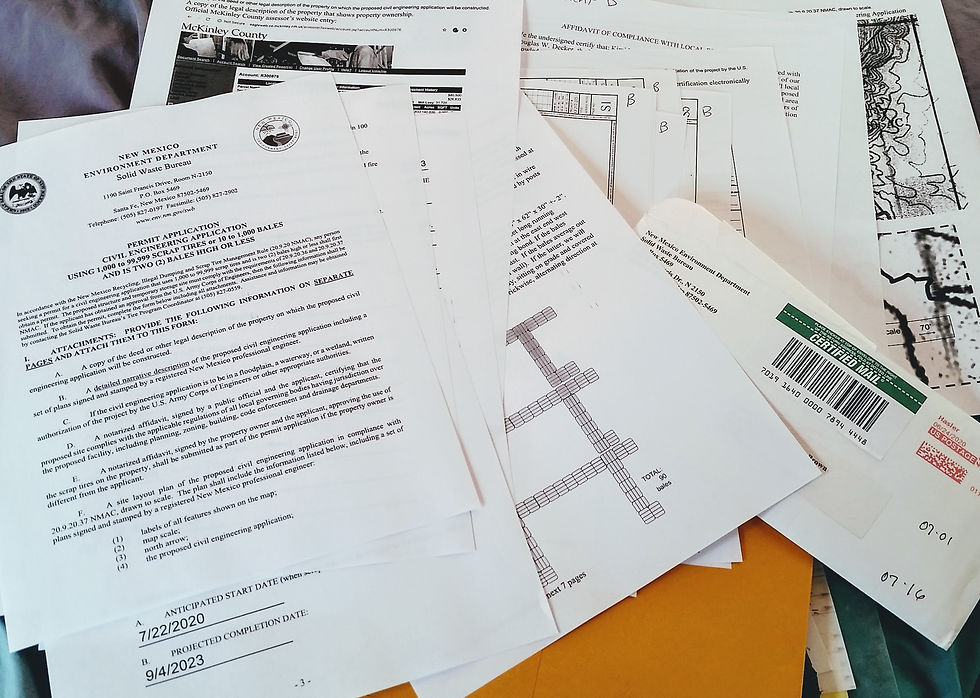
Meanwhile, I have been working on the tire bale permit. In addition to the building permit from the state Construction Industries Division, we need a separate permit for recycling tires from the New Mexico Environment Department Solid Waste Bureau Tire Management Program. Used tires are such a liability -- they are an eyesore, a potential mosquito breeding ground, a fire hazard, and can leach hydrocarbons and carcinogenic compounds into the groundwater and contaminate soil. As a result, environmentally-conscious states like New Mexico have strict requirements for tracking waste tires and monitoring their re-use. When we are granted our permit, each load that we pick up will come with a manifest that tracks the number of bales taken, and when we unload the bales we sign off on the manifest, take a picture for our records, and send it back for the landfill's records. We cannot store the bales on site since we don't have a location that qualifies -- 40 feet from grass and 100 feet from a piñon or juniper! No such place in this woodland. So as each load comes in, a forklift will unload in the house's "front yard" and then place each bale right into the house wall before the next load arrives. That's the theory -- a future blog post should show how that works in reality!
Our first tile bale permit attempt came back lacking. I re-wrote the application accordingly, and today we went to the county building in Gallup, picked up a required affidavit, signed and had it notarized, and mailed in our second try. When we got home we scheduled our “pre-pour” inspection, which will be on Monday -- and next week the concrete should be poured. We will pass our pre-pour inspection, and we will get our tire bale permit. Repeat after me: we will pass our pre-pour inspection, and we will get our tire bale permit.

Once the concrete is in (next week??) we will place two water tanks behind the north wall, and then, when our permit is in hand… time for TIRES!
We will pass our pre-pour inspection,
and we will get our tire bale permit!
[7/20 Update -- we did, indeed pass our pre-pour inspection, and we got word that our tire bale permit looks good and should be on its way to us on Friday!]
I should also remind folks that we are following on the coattails of Foxhole Homes (www.foxhole.org) who are building the first fully permitted tire bale building in New Mexico, the Shealy Shop (named after tirebale home pioneer, the late Mike Shealy). We learned of Foxhole Homes through the tire recycling program when we first looked into building a tire bale house a few years ago. Foxhole's mission is to build a community to house homeless veterans in Alamogordo, and they will eventually be building a whole community of passive solar tire bale homes!
UPDATE: Our inspector was out this morning and OKed the pour, and we just got the call that our tire recycling permit looks good, and after a few more signatures, it might go in the mail this Friday!!
Also, to answer your question, Jenny, we plan to build an earthen floor, yes!
Ross, our neighbor has suggested we take a geiger-counter to our stump, since the only place out here that he's found hotter than the general background noise in Albuquerque has been petrified wood... so we might not be parking our drinks there!
That stump is amazing! And everything else too!
Glad you are all well. It is so exciting! What will you use for flooring? Will it be rammed earth? Keep us informed and all my love to Ike. Be safe and continued best wishes.
Thanks, you all! Jenny, yes, I was glad/sad to hear that too. Relieved. I should figure out how to remotely volunteer. Maria, I'm hoping our crew will be the experts in the new tire-bale-home-building craze, hah! Jan, you are so nearby, we are hoping we will be able to see you out this way soon...