Plumb Tuckered Out
- Kimi BrownKawa
- Apr 7
- 9 min read
Chip is our electrician.
I am our plumber.
Chip and I have both done a fair amount of plumbing on our various remodeling projects on various houses over the years, each on our own before we met, and later together. He has done a lot more plumbing than I.
But I took on the plumbing job because I know nothing about electricity and little about framing, and I thought I knew something about plumbing. Ah well.
Off-grid plumbing
Rough-in
We initially pulled our plumbing permit in August, 2021. Our first inspection, the rough-in, would include everything under the finished floor level.
I hadn't worked with waste lines before (beyond sink p-traps), so the first thing I learned was that sanitary lines are much more finicky than I had expected. The slope angles have to be dialed in, and without a basement, we didn't have a lot of drop to work with. I started with the main line heading out through the foundation, and added on the feeder connections just before the exit. If you have done this, you can probably see that I used the wrong fittings, so a good chunk of the work below had to be re-done after our inspection, and became the inaugural pieces in my "hall of shame" pile of PVC that accumulated over the next 3+ years.
While I fiddled around with plumbing, Chip built concrete stem walls showing in that last photo, which would support the walls and the loft above.
An added complication to our off-grid waste plumbing was our split design, allowing greywater (anything but toilet or kitchen wastewater, which is considered blackwater) to be either routed to planting beds, or switched over to the main septic system. The black valves in the setup below are our Jandy switch valves, which will let us choose where to send the water.
We also needed separate greywater and blackwater cleanouts, and separate grey and black air vents out through the roof. And all of the waste lines had to maintain the 1/4" per foot slope as they combined and split in the twisting maze. Once glued, some of these also made it into my hall of shame and had to be redone to fix the slopes.

The above pic was taken in March 2022. The rough-in was built and approved in August 2022. As you may have read in a previous post, we were approved for an experimental worm septic system in November 2022, after a two-year struggle. If we had that permit in hand, I would not have bothered with the gymnastics of plumbing the grey/blackwater split, since all of our wastewater will be recycled sustainably. Still, it might help the worms (and future garden beds near the house) to have the greywater option, so maybe it's good that I got my "out" too late to take it!
In the photo above, the blue PEX lines curving up out of the PVC conduit are our bathroom supply lines that also pass under the finished floor from the utility room.
The pictures below show the utility room area. We had some pipes through the tire bale wall in the back, between bales. Two are PVC conduits for the supply main PEX lines -- one for each cistern we have in the back. One could be used some time in the future as a greywater line for a backyard garden fed by a washing machine, but for now it will just be plugged.
The utility room plumbing includes an emergency floor drain and vent, and a second drain and vent for a utility sink. There are also blue PEX supply lines: hot and cold for the bathroom, and hot and cold for the kitchen.
While I fiddled around with plumbing, Chip built the utility room walls shown in the last picture above.
The photos below show the kitchen rough-in plumbing: back-to-back sink waste heading over to join the main line beyond the front door. Yes, while I was messing with plumbing, Chip installed the sliding doors. In the first picture, you can also see the blue PEX supply lines from the utility room, and another supply line leaving the kitchen which goes under the floor to a hose bib through the west tire bale wall (out of the picture).
At our rough-in inspection, the inspector told us we needed to box in all of the waste lines in the floor. Chip built those boxes. We had a second rough-in inspection when that was finished (and my errors corrected), with a second inspector. In the last photos above you see the red cinders which form the next layer of our floor. We put those in to help achieve the required slope for this line. I'll write a separate post on our flooring process.
Top-out
OK, I thought the top-out inspection was where they looked at our plumbing vents connecting waste lines out through the roof. Oops. Really we were supposed to also have all of our supply lines done as well. I thought our vent lines could be horizontal as long as they didn't sag. Oops. Really we need to have them all sloped.
Our first (failed) top-out inspection was in July 2024... two years after our first (failed) rough-in inspection. I know that sounds crazy, but we (Chip) had to build two lofts, and we (Kimi) had to put the utility room and bathroom floors in, and install the bathroom lavatory before we could finish the venting. And we had a bunch of other stuff to do before we could do those things...
This is about where I hit my low point and headed to Albuquerque every week for therapy for a couple of months. I like designing and planning and even fighting for permits more than the endless slog of PVC plumbing! I can recommend EMDR therapy, but enough on that -- you can look it up if you want.
After our failed top-out, we had to install the supply lines, so we (Chip) also needed to finish more of the floor, so we (Kimi) could build the kitchen peninsula, so we could plumb the kitchen. But eventually we got there!
Supply lines
I was eager to move on to supply lines, which were more familiar ground. Still, there were some things to get my head around, since we are our own water utility. We loosely modeled our water processing on the Earthship Biotecture's Water Organizing Module (WOM). I took this picture at their visitor center outside of Taos.
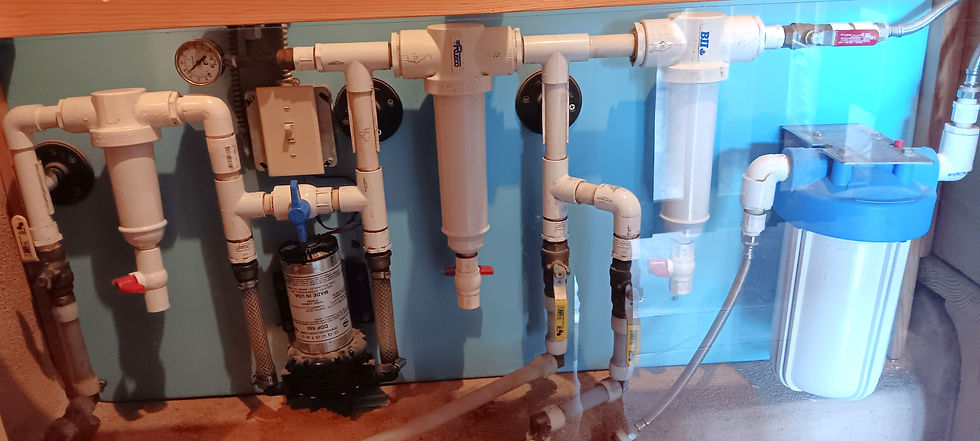
This was the funner part of plumbing, for me: researching, designing, planning, and assembling the supply. We had decided early on to use continuous PEX for the long runs through the bale walls and floor, and my more familiar copper in visible locations.
We have a little scaffold that I draped with welding cloth and used as a soldering bench. For larger sections I worked on big pieces of concrete backer board on the floor. I did call on Chip to do some of the more finicky joints on large pieces, or the joints in tight places next to our plywood sheathing. He has a better history with fire than I do, and is always ready to help.
I started in the bathroom. The PEX for the bathroom area came up just to the right of the lavatory cabinet. I switched to copper inside the cabinet for the sink faucets, mini tank heater, and a hose bib through the front wall. Under the left side of the cabinet floor, under an access panel, is the greywater/blackwater switch valve shown earlier.
In the bathroom area I did use a lot of PEX behind the scenes, going up through the walls and ceiling to the toilet and shower areas. The toilet supply has a thermostatic valve -- the t-shaped brass valve dangling in the wall in the second picture below. We will supply the toilet with slightly warm water. We will eventually install a Japanese-style sink on top of the toilet tank. Whenever we flush, the clean incoming water will flow through a faucet where we can wash our hands in the warm water, which then will flow from the sink into the toilet tank to be used for the next flush. Plus, then we will have warm water to supply a simple add-on bidet.
In the shower/bath room. I plumbed the shower controls. The shower's mini-tank heater will be installed in the adjacent closet. The hose bib also goes out through the 6-foot thick tire bale wall in the closet, to the covered area outside.
Below is our top-out in the utility room.
We have two water mains from the two outdoor cisterns. Each main has a coarse sediment filter. We can turn off either line independently, which will allow us to clean out one cistern without disrupting our water flow. After the filters, the two mains combine into one pipe which flows down to the pump.
The second photo shows the main utility working area. The black shallow well pump on the floor pulls water from the tanks and feeds it into the blue pressure tank, providing pressure to our whole house system. From the pressure tank, water travels through the two large filters: a fine sediment pre-filter, and then a 6-candle Rio 2000 ceramic filter by Doulton. After filtration, the water makes a U-turn through a water meter that we got because we are data-loving nerds and want to monitor our water use.
In the photo below, the four pipes coming straight out from the wall attach to the long PEX runs to the bathroom and kitchen: hot and cold for each. We don't have a whole-house water heater, so those pipes really all carry cold water from the utility room for now. We plumbed it to allow for both cold and hot, though, in case we ever feel the need to add a whole-house water heater in the utility room.

Eventually, cabinets were ready and it was time to plumb the kitchen. The PEX came up at the outside end of the peninsula, and another hose bib goes out at the opposite end through the front wall, so most of the cabinets had to have some plumbing in them. The cold supply splits in the first cabinet and sends another underground PEX line over to the tire bale wall, through which we installed yet another hose bib on the west side of the house. The heater cabinet has another thermostatic valve to increase our effective hot water.
You might notice that the cabinet centerline goes back and forth. That's because we didn't want to waste any cabinets on the "working" side of the peninsula, so we put the necessarily bigger cabinet dedicated to the heater and utility on the other side, where there will be an overhang and seating area -- less critical cabinet space.
Water source
We have had cisterns out back since 2020 when our foundation was done, and we plumbed them when we first installed the roof. They have been full-up and overflowing. We bought two larger cisterns which we will eventually swap out, but until then we are just using a transfer pump to move water around as needed. So far we have 6000 gallons in the tanks out back, and room for 2000 more.
Chip plumbed the tanks out back in preparation for hooking up the water to the house. He put in simple basket filters into the tank openings where the gutters enter. He then plumbed the valves with float intake filters, so that water coming into the house will be taken just below the surface, avoiding both floating debris and sludge at the bottom. Actually, in 4-5 years of sitting out there with open tops, the water is clear to the bottom. We don't have any leaf litter, and not even much dust has made it into the tanks.
Chip also wrapped the outdoor lines with heat tape. We do get winter here -- it can freeze between October and May, and it can get down to zero F, although daytime highs are usually 30-50 degrees warmer than nighttime lows. It isn't cold enough long enough to freeze our tanks, but definitely cold enough to freeze our lines.
Second top-out inspection
At last it was time to put our cards on the table. With Chip out back and me in the utility room, we turned on the water from the tanks. We can't hear through 6-foot walls and don't have phone reception behind our house, so we used the empty through-the-bales tube originally meant for laundry greywater as a tin-can-and-strings telephone to shout through. Turned out to be undramatic, though, no leaks up until the first shutoff, so Chip came in, and the scariest part was behind us.
Our first leak was, maybe not suprisingly, the outflow from the pump where lines are under pressure. We had connected the pump with a sharkbite push-to-fit, and it was leaking at the fitting. Chip rebuilt the section from the pump to the pressure tank, and we put in unions and conventional sweat fittings. After that, in our whole system there were just four threaded joints that needed a turn to stop seeping.
We flushed lines, hooked up filters and thermostatic valves, and flushed lines again, using our first 40 gallons... a week's worth of water, for us these days! We let it sit overnight to condition the filters. Pressure held. Then we called the inspector!
For our fourth plumbing inspection we had our fourth inspector. Nail-biting, since each inspector has had a slightly different take, which has always meant more work... it went swimmingly. He passed us and just gave us a couple of tasks to finish up. We sent him pics of our additional strapping, nail plates, and insulation later that same day.
Now, as with the electricity, we are in that fun testing phase! We have toilet, washing machine, and utility sink installed and working. We are temporarily hooking up a kitchen sink just to allow us to install the dishwasher (!)
Now we need to finish the lav and kitchen countertops so we can install sinks, and the big one: put in a mortar bed waterproof shower floor so that we can finish the shower room.
But now we have permission to finish insulating and closing walls which will take us a giant step closer to our final inspections!
Is there a light at the end of that tunnel yet??
I'm exhausted just reading about all this! How come the plumbing lines had to be boxed in? I'm glad it is all coming together for you.
So glad you sought out extra help
When needed. Therapy does wonders